Análise de OEE - Santa Klaus Factory
- SmartBI
- 26 de jan. de 2021
- 3 min de leitura
O OEE (overall equipment effectiveness) é o principal indicador utilizado para medir a eficiência global de um equipamento ou de um processo. Seu cálculo é realizado para responder perguntas como: qual o tempo de produção dos equipamentos? A capacidade de produção real é próxima da capacidade de projeto? A produção gera pouco refugo?
A resposta para essas perguntas ajudam a verificar a qualidade e o ritmo da produção.
No caso da SKF, o OEE foi calculado para a Produção. A área de produção é a que faz o link com o setor de compras e com o setor de logística de entregas. Esses três setores juntos compõem todo a cadeia de Supply Chain da SKF.

O OEE é calculado a partir da multiplicação de outros três indicadores: disponibilidade, qualidade e performance:
OEE = Disponibilidade x Qualidade x Performance
Cada um desses indicadores analisa diferentes pontos de um processo.
A disponibilidade é o indicador responsável por avaliar qual o tempo disponível para um processo ser executado.
A qualidade é aquele responsável por verificar o nível de refugos em um processo.
Por fim, a performance mede o quanto a capacidade produtiva se assemelha a capacidade de projeto.
A análise dos dados fornecidos pela SFK gerou os seguintes valores necessários para o cálculo do OEE:
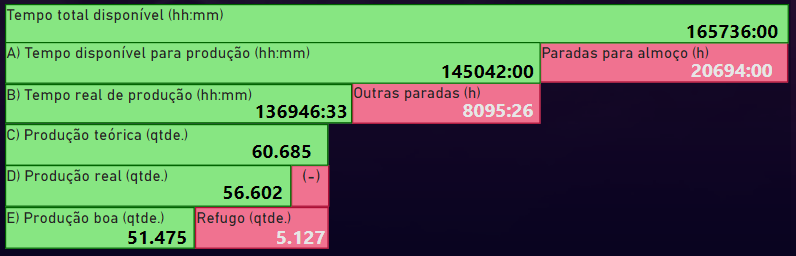
A partir dos dados acima, foi possível o cálculo do OEE da Produção da SKF. O resultado obtido foi o seguinte:

A disponibilidade é o resultado de B/A, onde A é o tempo total disponível, já consideradas paradas programadas, e B é o tempo real de produção, no qual foram consideradas as paradas não programadas. No caso da SKF, a única parada programada considerada foi a parada de 1h para o almoço. A performance é o resultado de D/C, onde C é a produção teórica e D é a produção realizada. E, por fim, a qualidade é o resultado de E/D, onde E é a quantidade de produtos refugada.
As paradas de produção que afetam diretamente a disponibilidade possuem 5 motivos distintos: refeição, falha operador, falha máquina, manutenção e limpeza.
O motivo refeição não está presente na análise final devido a um fato curioso observado na SFK. Existem operadores que excedem a parada programada de 1h para almoço, diminuindo a disponibilidade geral. Porém também existem operadores que não cumprem sua 1h de almoço, aumentando a disponibilidade. Comparando-se os dois casos, observou-se que as horas adicionais de produção creditadas pelos operadores que almoçam menos que 1h é maior do que as horas perdidas de produção pelos operadores que almoçam mais que 1h. Se isso fosse contabilizado na análise de paradas, o resultado traria horas negativas pelo motivo refeição. Dessa forma, a análise foi concentrada nos outros 4 motivos:


Para ter uma noção do impacto dessas paradas, pode-se fazer um cálculo simples que verifica quantos produtos seriam produzidos com essas horas paradas. Para isso, é necessário a produção horária média, que pode ser calculada por:
Prod.Horária = D/B = (Produção Real) / (Tempo Real de Produção)
Prod.Horária = 56,602 / 136,946.55 = 0.4133 [ProdutoAcabado/h]
Somando todas as paradas e multiplicando pela Produção Horária, obtém-se a quantidade de produtos que poderiam ser produzidos:
Produtos Perdidos = 8095.4 [Horas Paradas] * 0.4133 [ProdutoAcabado/h] = 3,345.95
Então, as paradas não programadas fez com que 3,345 produtos não fossem produzidos. Isso aumentaria, não só a disponibilidade, mas também a performance da Produção, o que aumentaria o OEE geral.
Uma análise semelhante pode ser realizada para o indicador performance, que trata o número de refugos na produção. Existem 3 motivos mapeados que categorizam os produtos refugados: peça amassada, erro programa e falha operador.
Os dados fornecidos resultaram nos seguintes motivos:


Uma análise final realizado pode ser realizado agrupando os motivos em categorias maiores. Tratando dos motivos de paradas, pode-se juntar os motivos falha máquina e manutenção em uma categoria maior de manutenção. Com isso, tem-se que 49.47 % das horas paradas possuem motivos relacionados a manutenção. Tratando agora dos motivos de refugos, pode-se juntar os motivos peça amassada e erro programa em uma categoria maior também de manutenção. Dessa forma, tem-se que 65.85% dos refugos possuem motivos relacionados a manutenção.
Portanto, pontua-se que a SKF deve dar uma atenção especial a manutenção em geral do processo, já que ele possui um impacto muito significativo no setor de produção da fábrica.
Comentários